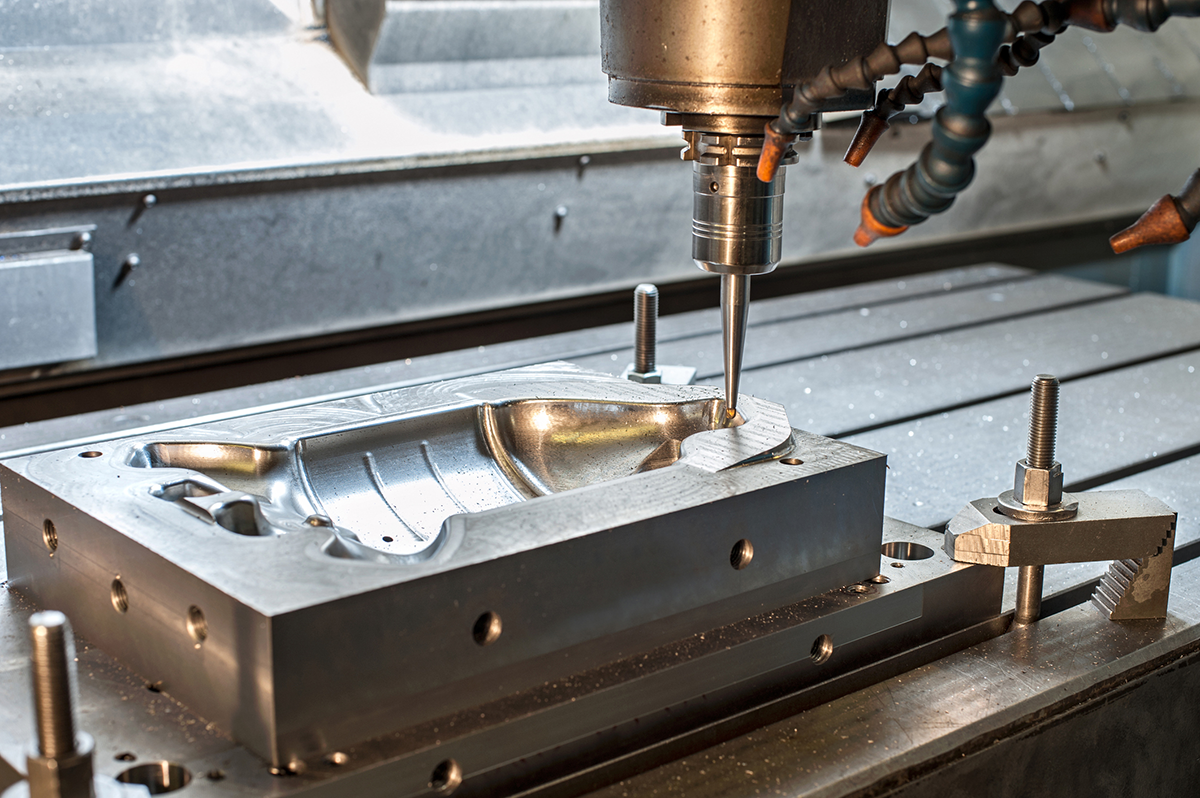
11. CONTROLLED INTRODUCTION, Part 2
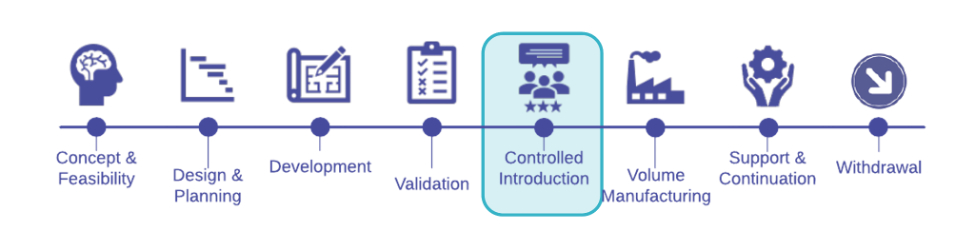
In our last blog post, we delved into the journey of transitioning from engineering and beta units to high-volume production. We explored the crucial steps of choosing a reliable contract manufacturer (CM), negotiating a mutually beneficial agreement, and providing comprehensive documentation to support the product assembly process.
Now, let’s dive into our next blog piece, where we’ll uncover the world of mechanical tooling options that will support your product’s successful development and scale-up into high-volume production. We’ll be exploring 3D printing, soft tooling, and hard tooling, each offering unique advantages and trade-offs. By understanding these differences, you’ll be empowered to make better informed decisions and select the best strategy to support your business.
Navigating Mechanical Tooling Options: Advantages and Trade-offs for Volume Production
Mechanical tooling options, including hard tooling, soft tooling, and 3D printing, present distinct advantages and trade-offs. Gaining insight into these differences enables businesses to make informed decisions and select the most suitable method for their volume production requirements.
3D Printing
3D printing offers the advantage of minimal lead times and rapid design iteration as well as no non-recurring engineering (NRE) charges, but typically comes with a much higher piece part price and may not produce parts with production quality. This technique is valuable for transitioning from product validation to production, especially for businesses not yet prepared for high-volume production. 3D printing serves as a viable option for limited quantities, ensuring design stability before committing to soft or hard tooling investments, provided that the aesthetics are not a critical concern for customer satisfaction.
Soft Tooling
Soft tooling presents a medium NRE cost, better quality parts, and a limited tool life (typically 10k to 100k hits) compared to 3D printing or hard tooling. With a lead time of 3-6 weeks for the tool, this option offers production-quality parts at moderate piece-part pricing. Soft tooling is a great choice for businesses looking to produce parts in limited quantities, while still maintaining quality and efficiency. This technique is well-suited for businesses that require a balance between cost, quality, and production speed as they transition from limited initial production to full volume.
However, soft tooling may not be suitable for applications where precise tolerances are required. Soft tooling materials, such as silicone or polyurethane, are flexible and can wear down faster than hard tooling materials. As a result, maintaining exacting tolerances may be challenging with soft tooling, and businesses should evaluate their requirements carefully before selecting soft tooling for their needs.
Hard Tooling
Hard tooling encompasses a variety of part fabrication technologies and typically uses high-strength steel or nickel alloys. This method provides high accuracy, precision parts with extended tool life (typically 100k to 1 million hits), lower cost per part, and production level quality. However, hard tooling often comes with longer lead times (usually 4-8 weeks lead time for the tool) and higher NRE charges. For high-volume production, hard tooling is generally the most cost-effective option.
Control and Cost of Tooling Development: Costs and Trade-Offs
When evaluating hard tooling development, it is crucial to consider factors such as offshore versus local production, direct control by Original Equipment Manufacturers (OEMs), transfer of control, and NRE costs (typically 50% upfront and 50% upon delivery). In some cases, suppliers will offer to amortize the NRE over the first-year of production to offset the upfront tooling investment, which will result in a higher per-unit COGS during the amortization period. These elements can significantly impact the overall cost model (with up to a 5:1 difference in toolmaker fees compared to the US, depending on the region selected) and schedule, necessitating careful evaluation to make informed decisions about the optimal approach for your product and business.
Fixtures and Jigs
Fixtures play a critical role in volume production as they hold and align parts during assembly or manufacturing processes. A well-designed fixture ensures high-quality parts with tight tolerances and excellent lot-to-lot repeatability. As companies transition from low to high-volume production, it is essential to have a strategic plan for incorporating fixtures into their processes.
Understanding the advantages and trade-offs of different mechanical toolong options is crucial for businesses to make informed decisions regarding their volume production methods. Carefully considering factors such as lead times, cost, quality, and control over development processes will enable the selection of the most appropriate tooling option tailored to your specific product requirements.
Next week, we pivot away from manufacturing and into business systems. Business systems are critical for agile hardware realization. They allow you optimizing processes, meet regulatory compliance, and scale your business. Follow Product Realization Group on LInkedIn and never miss a post!