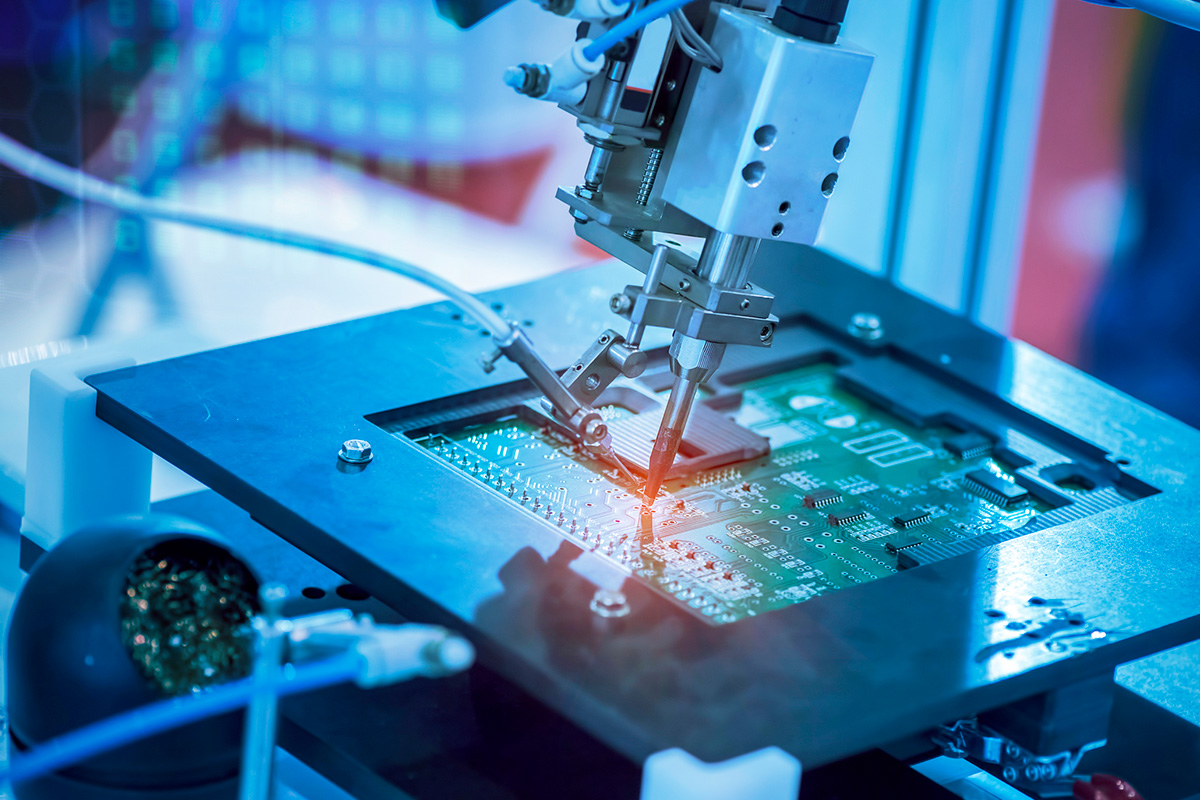
14. VOLUME MANUFACTURING AND BEYOND
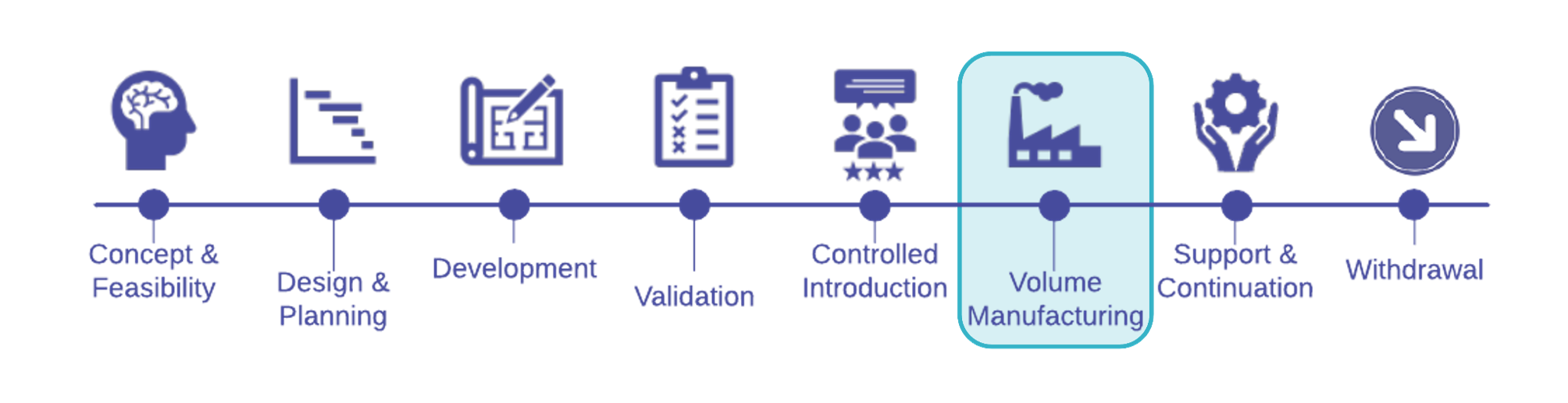
The Journey to Volume Manufacturing and Beyond: Scaling Your Hardware-based Product
In the span of our idea-to-scale series, we’ve navigated through the various phases of transforming a hardware-based product idea into a market-ready product. We’ve explored the crucial stages of design, planning, development, as well as controlled introduction. Now, we arrive at the pivotal point of Volume Manufacturing, where we will learn how it can be leveraged to increase efficiency, improve quality and lower costs to effectively scale your business.
In this final segment, we turn our focus to scaling a resilient supply chain and revisiting key concepts from earlier segments. These include Contract Manufacturer (CM) selection, tooling and fixturing, communication, and business systems. We’ll also include additional insights into production forecasting, test, and logistics and repair, with a focus on quality, delivery, and cost-effectiveness.
Building a Resilient Supply Chain
As you push towards volume manufacturing, significant funds are usually directed towards procurement and supply chain activities. Expect around 50% of company cash to be tied up in inventory during volume production. This financial investment is not usually recuperated until after sales, thus leaving a substantial portion of your cash tied up.
Therefore, understanding cost escalation as you scale your product is essential. For instance, making a change early in development results in minimal financial exposure, while making a change in volume manufacturing will have a much larger impact. This is dramatically different from software, where changes may be done at will with minimal cost impact. Think about the recent battery recall by GM, where 141,000 cars were recalled at a cost of $1.9 billion dollars combined with marked brand erosion.
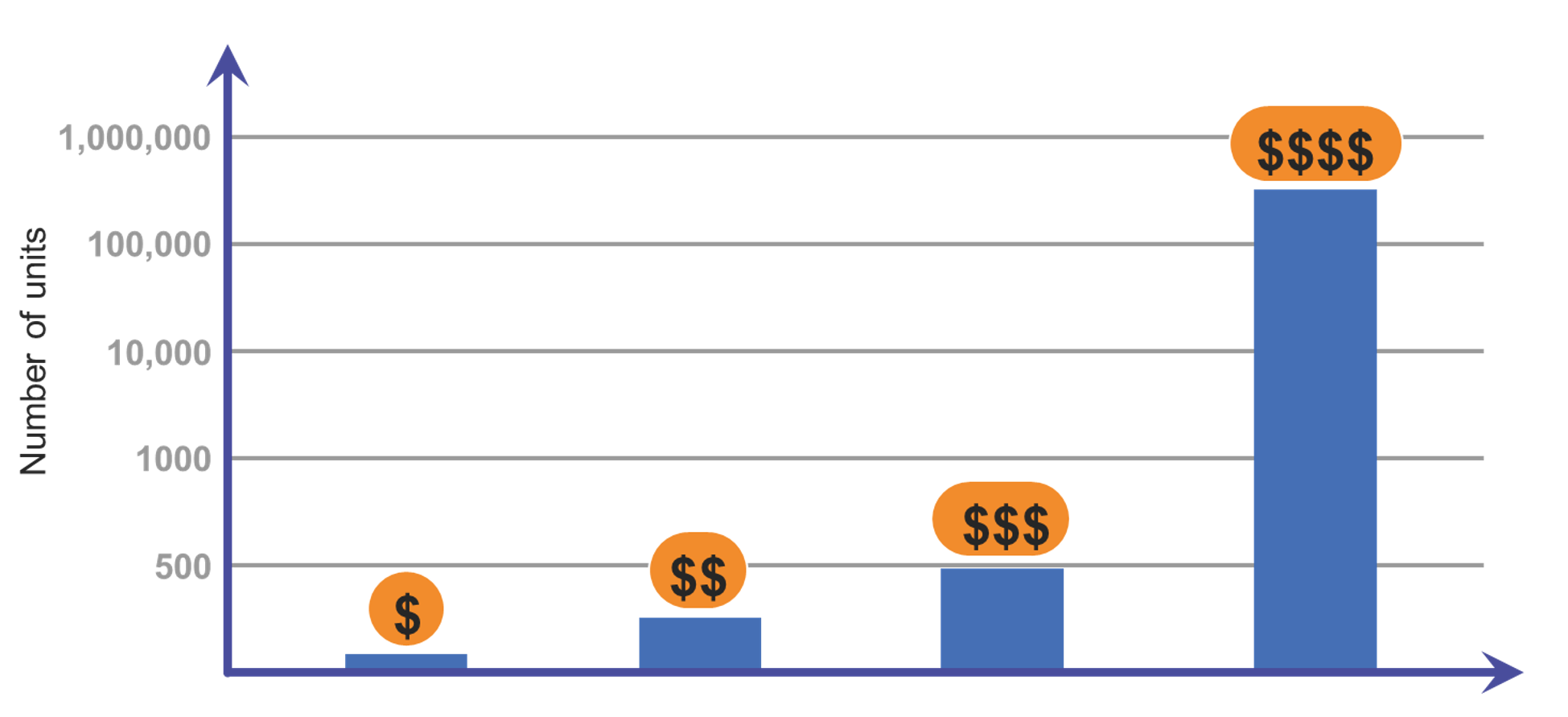
By following earlier recommendations in the series, you will have considered designing in parts that are easily available, cost effective, environmentally friendly, and high-quality. It’s also important to ensure that your volume suppliers can meet increasing demand, allocate sufficient engineering resources, production test coverage, deliver real-time yield and failure data reporting as well as support effective implementation of engineering changes. It is essential to provide clear and effective communications strategies ranging from forecasting, delivery of assembly and test instructions, to managing changes, parts deviations, obsolescence, as well as repairing and analyzing failed units.
On-site engineering support and regular business reviews should be properly resourced and include, at a minimum, a review of actual delivery, quality and cost relative to targets as well as process improvements and feedback to design for potential improvements. You should set up Key Performance Indicators (KPIs) early in the CM engagement process to monitor success. Key suppliers are an important extension of your business. By treating your suppliers well, it will be easier to scale in good times and mitigate supply chain risk in tough times.
In support of your journey to volume manufacturing, let’s review some of the earlier concepts shared in the idea-to-scale series.
Contract Manufacturer Selection, Contract Negotiation and Production Handoff
Choosing the right CM is a crucial decision as it can impact the success of your product launch, quality of your product, and the profitability of your business. Select the following link for a deeper dive into CM Selection, Contract Negotiation and Production Handoff.
Tooling, Fixtures and Jigs
Scaling to volume production often necessitates hard tooling, robust production fixtures and jigs. Hard tooling supports high volume production, high quality and low cost, while fixtures play a critical role as they hold and align parts during manufacturing processes. To explore tooling options, check out Navigating Mechanical Tooling Options.
Mastering Business Systems
Business scalability requires an effective business systems strategy. This includes software tools like Product Lifecycle Management (PLM) and Enterprise Resource Planning (ERP) systems. These systems help reduce errors, enhance reporting capabilities, enable effective change management and streamline demand management and planning. For a deeper look into business systems, see our earlier blog on Masterting Business Systems.
Conducting Effective Customer Trials
Unlike testing during the development phase, customer trials invite potential customers to try out your product in small, controlled groups of users to provide feedback on the product direction. Customer trials are conducted before signing off on volume production. Refresh your understanding in our last blog on Customer Trials.
Implementing a Production Forecasting System
To support volume manufacturing, it is essential to establish a flexible forecasting system that allows you to adapt to changes in demand and adjust your production schedule. Inaccurate forecasts can result in either over production (excess materials) or under production (not being able to fulfill orders and collect revenues), so putting in robust forecasting systems that will provide accurate forecasts, and monitoring these on a frequent basis, are essential to managing costs effectively and fulfilling customer demands.
Executing a Production Test Strategy
Production testing is critical for supporting volume production and is often the bottleneck to throughput. To verify that your product meets requirements and debug to the root cause, you should incorporate multiple layers of testing in volume production. Testing should be incorporated early in product design as it is not easy to add test points after the design is complete.
Some levels of test to consider in volume manufacturing include:
- Board level: Design in-circuit (board-level) tests for printed circuit boards.
- Sub-System: Perform sub-system functional (board and system level) testing.
- System: Perform full system level functional testing.
- Whole Product: Perform full product level testing (including software).
- Burn-in: Used to induce failures in manufacturing and reduce field failures.
Planning for Order Fulfillment and Logistics
Getting products from your factory to end customers is often an overlooked and underestimated activity that should be included as part of your product realization strategy. The following factors may impact how you implement your fulfillment and logistics strategy.
- Type and size of product
- Product structure, configurations and accessories
- Industries and locations served
- Production volumes
- Return and repair strategy
If you have multiple sub-assemblies built overseas, you may want to consider engaging a “last-mile” fulfillment house that can support limited final assembly, test, labeling and shipping to end customers. These fulfillment houses generally have effective business systems to keep track of product shipments to customers as well as the management of returns and repairs.
Ensuring Reliability and Quality
In volume manufacturing, product reliability and quality are critical to your success. A solid reliability strategy will ensure that products will meet the desired reliability target. Tools like Failure Modes and Effects Analysis (FMEA) and Highly Accelerated Life Testing (HALT) in design, and Highly Accelerated Stress Screening (HASS) in production can help to ensure the reliability of your product. In addition, first-pass yield in the factory should be a priority metric, indicating the number of products manufactured correctly the first time, and used to help identify and mitigate failures.
Implementing a Cost Reduction Strategy
To remain competitive, a cost reduction strategy is essential. This could involve sourcing cheaper parts, incorporating automation testing, and most importantly revising designs. For many products in volume production, manufacturing is responsible for a much smaller portion of cost reduction opportunities relative to re-engineering the product for lower cost.
In closing, the journey to volume manufacturing is long and loaded with unforeseen challenges as well as opportunities. With proactive planning and investment, effective business systems, and a strong commitment to quality, you can successfully bring your product from idea to scale. This final stretch of the journey requires a complex balance of many elements, but when executed correctly, it’s a rewarding final chapter in your product’s journey from concept to scale. However, your remarkable journey doesn’t end here. It’s a continuous loop of learning, iterating, and improving – always staying innovative and agile in a highly competitive and rapidly evolving market landscape.