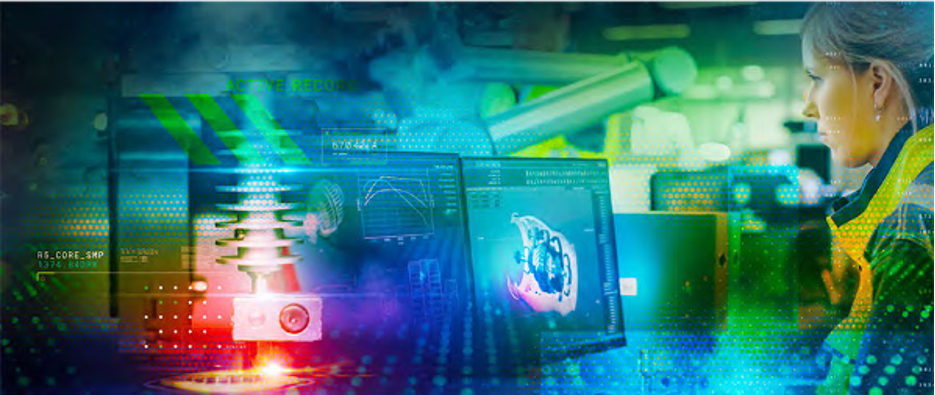
12. CONTROLLED INTRODUCTION, Part 3
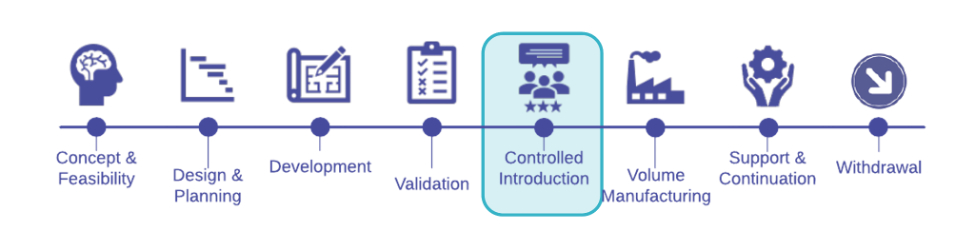
In the last blog, we discussed how to navigate the various mechanical tooling options and the advantages and trade-offs for volume production. We learned that considering factors such as lead times, cost, quality, and control over development processes is essential to selecting the most appropriate tooling option tailored to your specific product requirements.
Now, let’s continue to our next blog series, which will focus on business systems. Business systems are critical for supporting agile product realization, optimizing your processes, meeting regulatory compliance, and scaling your business. So let’s explore business systems strategies, flows, usage throughout the product life cycle, and tips for success.
Mastering Business Systems: Strategies for Agile Product Realization and Scalability
The Perils of Manual Processes and the Importance of Effective Business Systems
Manual processes are inherently error-prone and create isolated silos of information, which slow down your New Product Development and Introduction (NPDI) process and impede your ability to share information between internal groups, external partners and suppliers.
Without effective database tools, for example, your product data will be subject to “institutional knowledge,” which means that if you lose key development resources, you may also lose your data. Also, there is no way to effectively search your data in silos, so having information readily available for development, regulatory and/or customer audits will be difficult to impossible. Finally, strong project management and key performance indicators can be enabled with business systems, which will support a faster, more agile process that is more cost efficient.
As your product moves through the product life cycle, you will find an increasing need to shift from flexibility in the concept phase to greater control as you approach volume production, where you will need to share increasing amounts of product data across organizational boundaries. Implementing systems that are easy to install and manage–ideally cloud-based–will provide the infrastructure required to scale your business and support an agile hardware NPDI methodology. Some of the most important business systems for hardware-based products include:
- Customer Relationship Management (CRM): CRMs are designed to help businesses manage, monitor, and optimize customer interactions. They centralize data, automate communication, and provide tools to improve satisfaction, retention, and sales. Streamlining sales, marketing, and customer support, CRM systems foster stronger customer relationships.
- Electrical CAD (eCAD): eCAD is a system that assists in designing electronic systems like PCBs and integrated circuits. Engineers can create and modify diagrams, layouts, and 2D/3D models using eCAD. Also known as electronic design automation, it generates raw parts data that feed into downstream activities.
- Mechanical CAD (mCAD): mCAD aids mechanical engineers to create precise raw parts as well as product designs and technical drawings (2D/3D models) for engineering and manufacturing use.
- Software Management Systems: Embedded software and firmware tools include platforms for the development of software programs that are embedded into hardware systems using standard operating systems, languages, and tools.
- Product Lifecycle Management (PLM): PLM systems manage the product records, streamlines the NPDI processes, fosters cross-functional collaboration, and ensures regulatory compliance throughout a product’s lifecycle. It organizes raw parts data from eCAD, mCAD, and software into a full product record, and communicates with internal systems like ERP and CRM, as well as external suppliers and Contract Manufacturers (CMs).
- Quality Management System (QMS): Documents processes, procedures, and responsibilities to achieve quality goals. It manages quality and training records to meet customer and regulatory requirements while enabling a Closed Loop Corrective Action (CLCA) process.
- Enterprise Resource Planning (ERP): ERP systems manage manufacturing, logistics, distribution, inventory, shipping, invoicing, and accounting. They streamline various business activities, including sales, marketing, production, inventory, quality management, and HR. ERP systems utilize product information from PLM or CAD systems, adding data like part cost, lead time, and lifecycle to support the materials management process.
Optimizing Data Flows through the Product Life Cycle
Imagine the flow of product data as it travels through the various business systems, similar to the NPDI process flow. An effective integrated business systems strategy will clearly specify where data is created, which systems it is replicated, how it is controlled, and automate the data exchange between systems. It will also support the creation of workflows, key performance indicators, and change management.
Figure 1.1 illustrates a typical flow of data between systems in an Original Equipment Manufacturer (OEM) through communication with a CM.
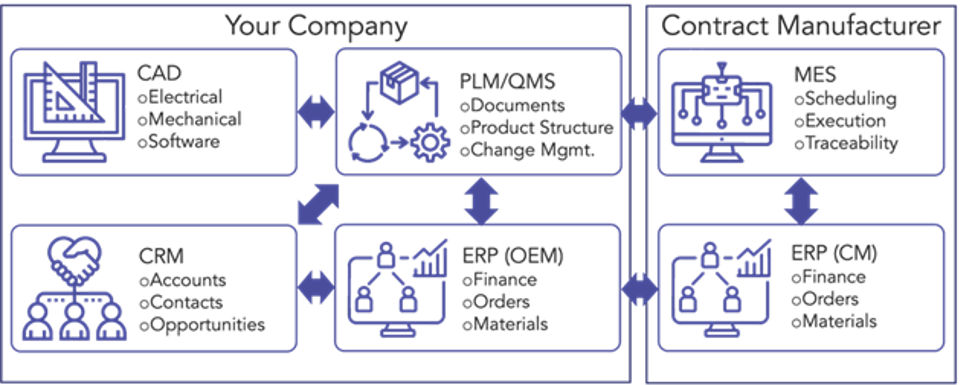
Managing Product Data Across Business Systems
Once you establish an automated systems infrastructure, it is common for many product data elements to be duplicated across different business systems. Take part numbers as an example; they are generated in engineering, but also utilized in PLM, ERP, CRM, and MES systems. To adhere to good database management practices, unique data elements should be controlled within a single system, even if they are replicated in others.
When properly architected, data can be created in one system and automatically duplicated seamlessly into other systems through an automated process. Identifying which systems serve as the “data master” (originating and controlling data) and which function as the “data copy” (duplicating data from the data master) is critical to your data management strategy.
Figure 1.2 provides a real-world, partial customer example of how this mapping can be accomplished.
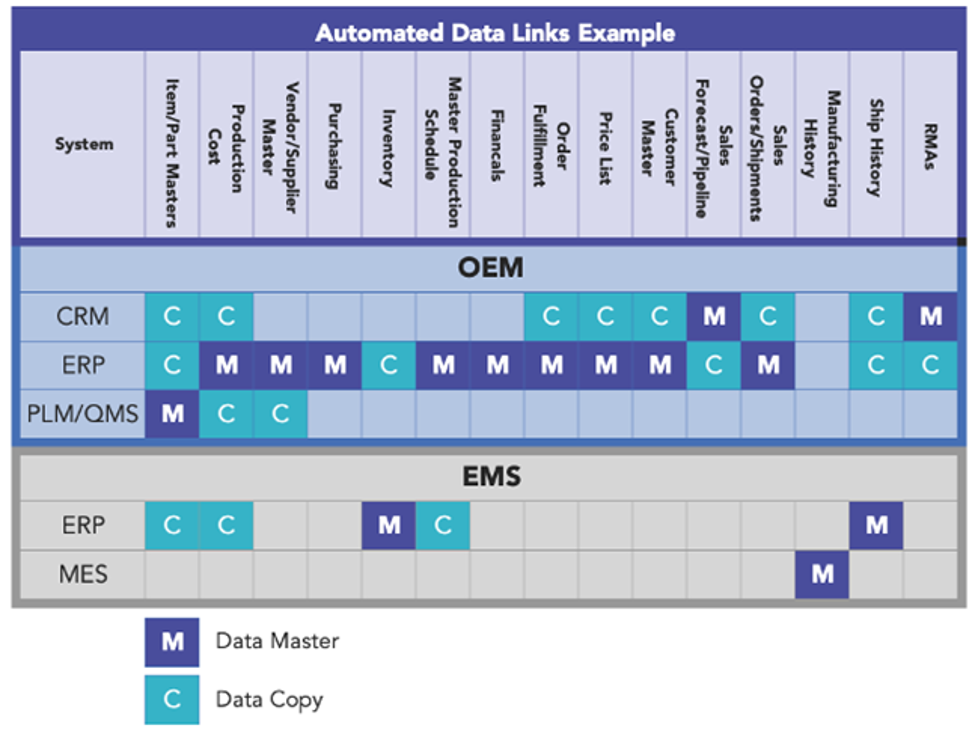
7 Tips for Successful Business Systems Deployment
Now that you have a better understanding of the importance of effective business systems throughout the life cycle, the risks of manual processes, and the benefits of an integrated systems strategy, follow these recommendations to ensure a successful business system deployment.
- Develop an end-to-end systems strategy, considering collaboration both internally and with outsourced partners, as well as data flows between systems.
- Secure management commitment and support before investing time and resources.
- Install most critical systems first and phase-in additional systems to enable business growth (typical order is PLM, ERP, CRM). Utilize SaaS platforms when possible for scalability and ease of management.
- Allocate time and budget for process definition, training, and automation of data exchange to improve efficiency.
- Appoint a dedicated project manager and provide ongoing support resources.
- Establish clear statements of work and create service-level agreements with software vendors.
- Ensure ample end-user training, and reserve a budget for vendor support and systems update management.
In conclusion, when constructing a business systems strategy, begin with the end in mind, and understand the importance of business systems and their impact on agile product realization as well as scalability. By implementing a robust business systems strategy, your organization can streamline its processes, improve collaboration, and better meet customer and regulatory requirements. As a result, you will be well-equipped to navigate the complexities of hardware-based product development, enable scaling into volume manufacturing, and thrive in today’s competitive market landscape.
Next week, we continue the product journey into customer trials. Customer trials help you to gain early feedback on the product in a small, controlled audience. This feedback can then be used to validate the current product, or feedback back user issues into the development process that will be incorporated to better support full market scale.