The SV Hardware Startup to Scale Meetup had a panel on Medical Product Development & Manufacturing on April 4, 2017 at Evolve Manufacturing in Fremont, CA. Panelists included: Jordan Bajor, COO of Gynesonics, Inc., Tom Geraty, Senior Designer at Fusion Design™, and Noreen King, President and CEO of Evolve Manufacturing.
One of the recurring themes during the program was the role of human factors in medical device development.
FDA Approval of Medical Devices Requires Human Factors
Understanding how people interact with technology and studying how user interface design affects the interactions people have with technology is the focus of human factors engineering (HFE) and usability engineering (UE).
As described on the Food and Drug Administration website, human factors and usability engineering considerations in the development of medical devices involve three major components of the device-user system:
- The device users
- The device use environments
- The device user interfaces
The interactions among the three components and the possible results are depicted below in the figure below (from the FDA website):
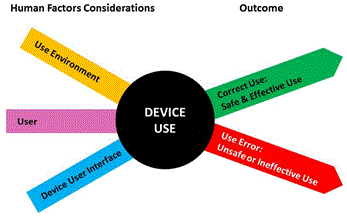
The FDA is concerned with two areas of human factors with respect to medical devices: device safety and device effectiveness. Device effectiveness is evaluated according to its intended use. Human factors requirements for medical devices are usually addressed in the design process as part of 21 CFR Section 820.30 “Design Controls.”
- the manufacturer must establish design and development processes; (sec 802 (b))
- the manufacturer must gather design requirements relevant to both the patient and the user; (sec 802 (c))
- the manufacturer must define procedures for compliance to requirements; (sec 802 (d))
- the manufacturer must conduct design reviews; [(sec 802 (e))
- the manufacturer must establish procedures for design verification: Did I make the product right? (sec 802 (f))
- the manufacturer must establish procedures for design validation: Did I make the right product? (sec 802 (g))
Involve human factors as early in your design process as possible.
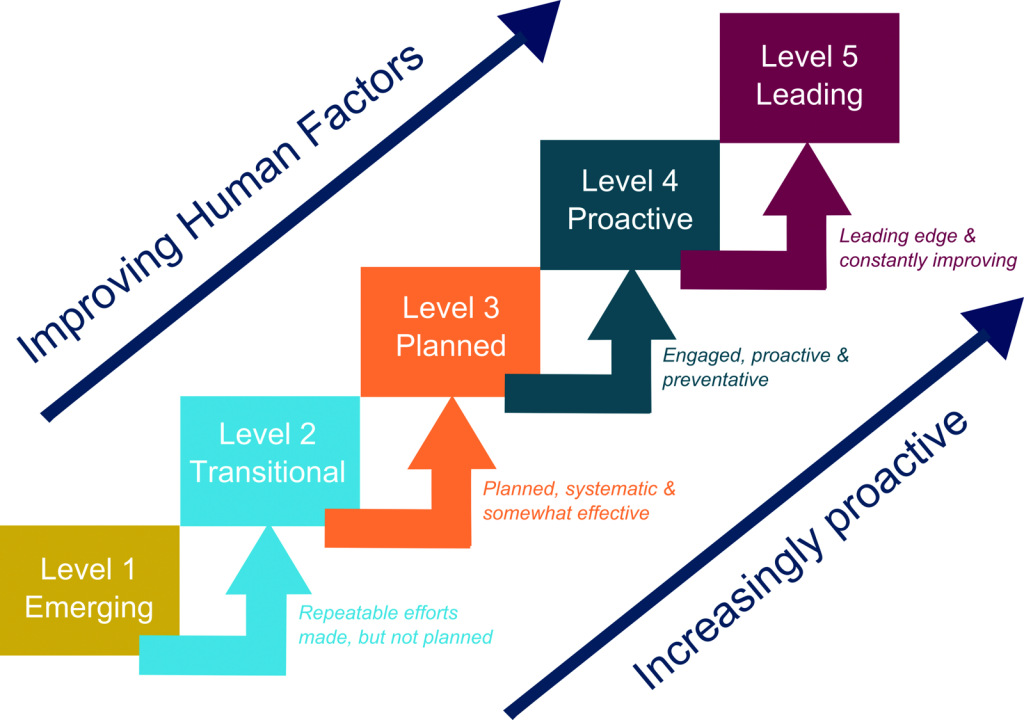
According to Jordan Bajor, it used to be that the original medical device designs were for “cowboys,” the high-visibility MDs, not the end user or customer. Because a company is now required to complete a third party human factors analysis as part of FDA approvals, human factors engineering is incorporated into the design process. As Jordan explained, it’s not just how a knob feels to the doctor.
The FDA requires that the product is safe and effective for its intended use, so your product must be tested with your labels and your instructions against your intended end users. And you have to test the filed device, not a prototype. Jordan advised to make sure to budget both the money and the time for these requirements. (They budgeted $200k for 6 months). Also, make sure to work with a reputable testing group that is familiar with the process and that can stand by its report.
Who is the user?
With many medical devices moving into home use, the ultimate end user is the patient, not the doctor. Tom Geraty of Fusion Design noted that the design considerations are large when you start to look at product use from the vantage of patient versus the doctor. Fusion Design worked on a device for migraine sufferers and diabetic insulin pumps. Noreen King, CEO of Evolve Manufacturing, recently visited a client who is developing a home dialysis unit. The client handed her a system to set up, which she was able to do within 20 minutes. The client wanted her to understand that the product was intended to be used by someone just like her.
The key is to catch human factors issues early when the cost to make a change has less impact on the production process. Jordan explained that the Gynesonics industrial designers worked with male gynecologists to develop their first device. In fact, their target users were female gynecologists, who complained that the device was too large and too heavy for their smaller hands.
Technology Advances in Human Factors
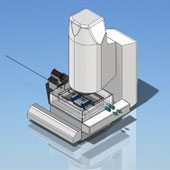
Some perceive a tension between the highly regulated medical device environment and the need to be lean, efficient and iterative. Human factors engineers like to get their hands on the product and test. However, there are opportunities to involve human factors engineers early with the industrial design team. Advancements in development tools enable early and less costly iterations. All three panelists agreed that one of the biggest changes in medical device development has been the widespread availability of more affordable development tools like Computer Aided Design (CAD) and 3D printing to enable rapid prototyping. According to Tom, they take a broad approach with their industrial design teams. They try to identify the highest priority product factors and features. The process is faster but not the same as having the end user to shape things. If they need to create a model of something that needs to be malleable, they’ll use something like clay. Noreen explained that they no longer need to do molds for parts because of 3D printing. They are able to get parts in days (versus weeks or longer) and do rapid prototyping for clients. With tools more affordable and available, and rapid prototyping, Jordan explained they are able to make design decisions more quickly and with less investment.
Mitigate Risk
The FDA sees human factors engineering and user interface design as essential risk management practices for medical device development. The risk analysis:
- identifies anticipated use-related hazards and possible unanticipated use-related hazards;
- develops and applies measures that eliminate or reduce use-related hazards resulting in harm to the patient or the user; and
- demonstrate whether the final device user interface design supports safe and effective use.
Risk management and reduction in medical device development was another theme repeated by all three panelists.
New Rules for Medical Device Funding
Startup success for a medical device company is no longer measured by a pure technology, that is, a proof of concept and some data that can then be acquired prior to FDA approval. Investors and venture capital firms now expect a medical device startup to bear greater business risk and be able to develop not only for safety and efficacy, but to plan, show value, and build all the way to scale prior to an exit.
Additional Resources
Resources on medical devices and human factors engineering:
- Human Factors and Medical Devices (FDA Article)
- Story, Molly Follette, PhD., FDA Perspectives on Human Factors in Device Development (June 7, 2012)
- Applying Human Factors and Usability Engineering to Medical Devices, February 3, 2016.
- FDA information on medical devices
Comments? Questions? Join the conversation on Facebook!