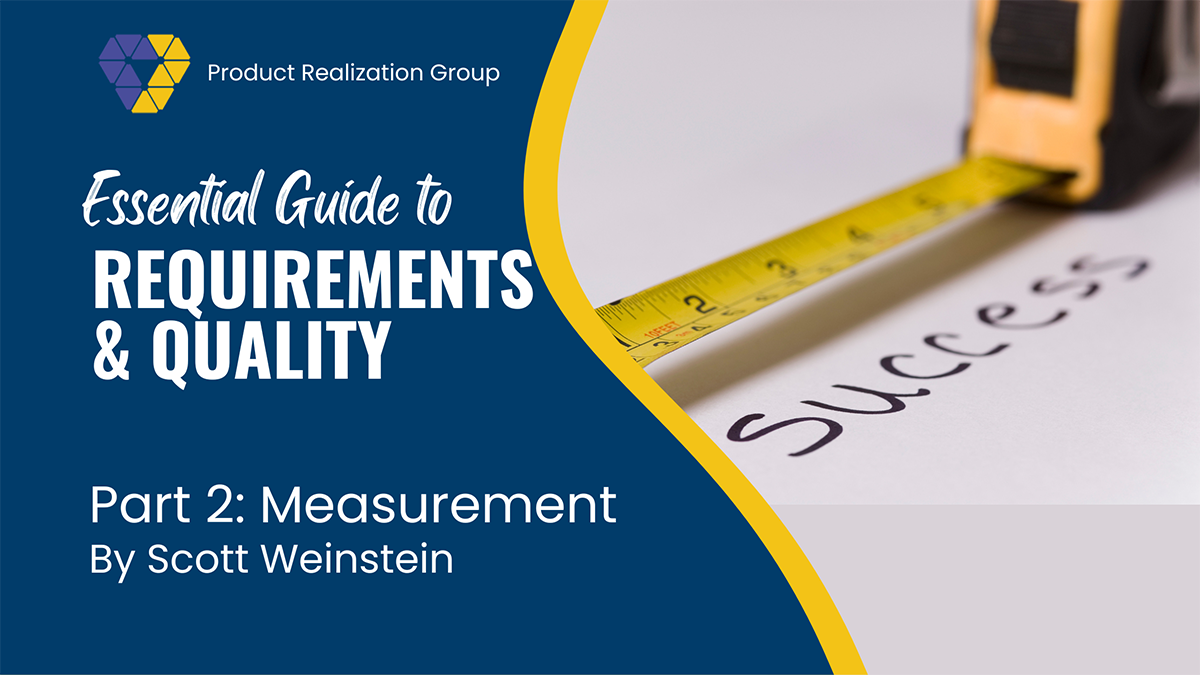
Hierarchical Requirements Definition
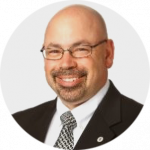
Scott Weinstein, Quality & Reliability, Principal Consultant at Product Realization Group
Scott Weinstein is a hardware development and manufacturing veteran with 25+ years of experience leading quality and reliability engineering programs at global companies, including Roku, Ford, Whirlpool, Keurig, Sonos, Harman, and Johnson Controls. A quality leader, Scott specializes in product design and operations for high-tech hardware companies. Scott has an MBA from the Worcester Polytechnic Institute and a Bachelor in Electrical Engineering from the Georgia Institute of Technology.
Measuring quality is essential, but it may not be effective without first defining requirements. To do so, many experts use a hierarchical approach. This approach allows for a thorough evaluation of all necessary aspects, leading to better overall outcomes. Therefore, effective quality measurement can be achieved through hierarchical requirements definition.
Last week, Scott Weinstein, an expert from the Product Realization Group, emphasized the crucial link between quality and requirements. This week, learn how to define requirements and measure quality, providing actionable insights that will boost your product’s performance.
How Should Requirements Be Defined?
So, in order to measure quality, you first need to define the requirements. I always use a hierarchical approach to requirements definition. The hierarchy I typically use is as follows.
- Product Requirements – are the customer-facing requirements. These are usually defined by the Product group and describe the product in terms of customer needs, wants, and desires. In some industries, much of this could come directly from the customer, such as a tier 1 automotive or aerospace supplier. In other industries, they would be completely defined by the manufacturer, like in the consumer products industry. But regardless of industry, some requirements will come from government agencies like health and safety, and environmental.
- Engineering Requirements – define the product from an engineering perspective in order to meet the Product Requirements. These are defined by the engineering groups (electrical engineering, mechanical engineering, software, quality, etc). They go to the next level of detail below the Product Requirements and should have a hierarchical relationship with the associated Product Requirement. This could start with developing a functional block diagram, the functions associated with each block, and then the requirements for each functional block. This method works well with a modular architecture design approach.
- Manufacturing Requirements – define the process requirements that will be necessary to meet the Engineering Requirements. These are defined by the manufacturing organization (manufacturing engineering, testing engineering, manufacturing quality, etc). They should define the process parameters and product characteristics that should be controlled during manufacturing in order to meet the engineering requirements. A helpful tool to use here is a correlation matrix looking at the engineering requirements versus the process parameters and product characteristics and identifying the strength of the correlation between each of them.
Once you’re through the Concept and Feasibility stages of New Product Development, then the Product group can develop the Customer Requirements. These are the high-level requirements, generally from the customer’s perspective. They can include things like level of performance, overall physical size, number and types of inputs and outputs, usage and storage conditions, product lifetime, etc. These requirements could also have priorities assigned, like Must-have, Should-have, and Could-have. This way you can make it clear to engineering what is most important when engineering trade-offs need to be made.
Then the Customer Requirements can be used by Engineering to develop the detailed Engineering Requirements. These should be very precisely defined, with enough details that design decisions and trade-offs can be made, as well as develop the verification and validation test methods. So instead of just stating a parameters value with associated tolerance, it would also include the associated operating conditions and measurement method. This could either be an industry standard test method or just an internal company method. And keep in mind, not all requirements will have a quantitative measure, there will also be requirements that just describe how something should work, like a user story, or a specific material or component that will be used. But either way, it should be precisely defined.
Finally, the Engineering Requirements can be used by Manufacturing Engineering to develop the detailed Manufacturing Requirements. These requirements will include the manufacturing processes needed to fabricate and assemble the product, the process parameters that need to be controlled, the product characteristics that need to be tested, and the associated test and measurement equipment for the process parameters and product characteristics.
During the development of the Product, Engineering, and Manufacturing Requirements, Special Characteristics should also be identified. These Special Characteristics, both Process Parameters and Product Characteristics, can be categorized as follows.
- Critical Characteristics (CC) include those characteristics that are associated with Safety and Government Regulatory requirements. This could include something like a tip-over angle to minimize the change of a product falling over on a child or a maximum unwanted electromatic interference (EMI) that could interfere with the operation of other products nearby, like a cell phones, radios, or medical devices.
- Significant Characteristics (SC) are important characteristics, that are not related to Safety or Government Regulatory requirements, but do have a strong correlation to customer satisfaction. Therefore, variation in a Significant Characteristic would have a perceptible change in performance for the customer or user. This could include standby current or operational current of a product resulting in a higher than expected monthly electrical bill or even a dimensional requirement that if it varies too much, won’t fit or mate correctly with another product, like thread pitch on a bolt.
Identifying and categorizing special characteristics is helpful in identifying the control methods that should be used for each characteristic. Since Critical Characteristics are related to Safety and Governmental Regulatory requirements, every product produced needs to meet this requirements, so 100% inspection or test should be employed or some form of mistake proofing. For Significant Characteristics, which are important to customer perception and quality, these characteristics should be controlled using Statistical Process Control (SPC) or closed-loop control systems.
By defining requirements using a hierarchical approach, one can effectively measure the quality of a product or service. This approach ensures that all necessary aspects are considered and evaluated, leading to better overall outcomes. Next week we cover the best tools to develop and measure requirements.
Attempting to assess the quality of a new product without the necessary requirements is akin to driving to a new location without a map. Although you may have a general idea of the directions and may ultimately reach your destination, it will be a faster, less expensive, and easier journey if you use a map. Please join us next week for an in-depth analysis of how requirements should be defined for the best business outcomes.
Are you curious how to improve your hardware product’s quality and reliability? Contact us for a free consultation today. Or read on and learn more about Agile hardware development from the experts at Product Realization Group.